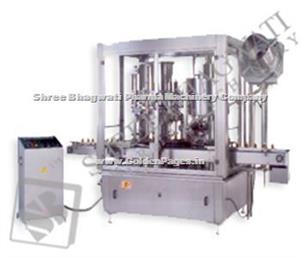
Automatic Rotary Piston Filling And Capping Machine
Description:
"GMP" Model based on advanced technology.
Single Operator for Two Operations.
Less Floor Area - as both the sections driven by one motor.
No Contamination as immediate sealing of filled bottles.
Accuracy ±1% due to piston dozing principle.
Centralized Volume Adjustment System.
No Bottle No Fill for individual head, hence no spillages.
Placing of Cap Feeder Outside Monoblock-avoid entering of dust in it.
Fewer Caps in chute automatically stop the machine.
Additional Sensors for Minimum and Maximum Level of Cap in chute which automatically start and stop rotary cap feeder to avoid Damage of caps during Rotation and Wastage of Energy.
Better finish imported polished, laminated S.S. sheet used.
Electronic liquid level controller and pneumatically controlled control valve.
Drip trays under the conveyor.
Self Lubricating UHMW- PE Guide profile for Low friction wear surface, smooth and noiseless conveying.
Universal coupling for quick and easy setting of In-feed worm.
Safety Guard for Operation and Protection.
Electronic Sensor at out feed for Bottle Jamming.
Optional Features :
Motorized Height Adjustments.
Automatic chain washing system for conveyor belt.
In-built pre-inspection.
Nitrogen Flushing.
Cap Elevator to feed caps to the feeding bowl.
Technical Apecification:-
Model SRPM - 6/6 SRPM - 8/8 SRPM - 16/8
Output/Hour 2500 to 7500 Bottles 4000 to 10,000 Bottles 7000 to 14500 Bottles
Number of head/syringe 6 8 16
Number of head/syringe 6 6 8
Direction of movement Left to Right
Fill Size 30 ml. to 200 ml.
Electrical Specification Main Machine 3 HP / 415 Volts / 50 Hz. 5 HP / 415 Volts / 50 Hz.
Oriental Bowl 0.25 HP / 415 Volts / 50 Hz. 0.5 HP / 415 Volts / 50 Hz.
Conveyor 0.5 HP / 415 Volts / 50 Hz. 0.75 HP / 415 Volts / 50 Hz
Height of Conveyor 910 mm to 960 Adjustable
Machine Dimensions 3050 mm (L) x 1400 mm (W) x 2200 mm (H) 3660 mm (L) x 1700 mm (W) x
2400 mm (H)
Case Dimensions 3250 mm (L) x 1600 mm (W) x 2200 mm (H) 3850 mm (L) x 1900 mm (W) x
2400 mm (H)
Net Weight 2500 Kgs. 2650 kgs. 4200 Kgs.
Gross Dimensions 3000 Kgs. 3250 Kgs. 5000 Kgs.
Change parts required A) Container: Star Wheel, Back guide, Feed Worm, Nozzle (B) Cap: Die, Delivery chute, bowl. (c) Syringes (if
volume higher/lower then above specification)
* Depends on fill size/ nature & viscosity of liquid
**We can supply as per client's requirement
***with the help of change parts
Gravity Filling Machine:
Gravity filling system is simplest and efficient filling system for non carbonated liquids, like vacuum filters, these fillers also maintain same level while filling particular size adjustment and fill by gravity principle. It is used for filling only non carbonated liquids. Gravity fillers are available in options of with and without partial vacuum depending upon applications.
Direct contact of filling tank and filling nozzles both in stainless steel avoids plastic tubings. Thus, no chances of contamination, easy cleaning and change over from one product to another.
Vacuum Filling Machine:
Vacuum filler is a rotary level filler which fills with vacuum principle and maintains same level while filling particular size adjustment. It is used for filling only non carbonated liquids.
Applications:
To fill-liquor, pharma liquids, household liquids in glass rigid bottles and containers.
Salient Features:
Machine is of simple design and with very less moving parts. Thus, easy to maintain.
The bottle lifters are mechanical spring loaded. .
All Change parts made out of UHMW.
Centralized lubrication.
Capable of handling bottles of any shape and size.
Speed variable with variable speed pulley. However, AC frequency drive can also be provided at an additional cost.
Inbuilt conveyor with overlapping at out feed end driven by imported speed variator.
Higher models fitted with automatic overflow system.
Safety hood aluminum S. S. frame with toughened glass can also be provided at additional cost.
Easy change over from one size to another.